Tech Out: Don’t sit on the top tube
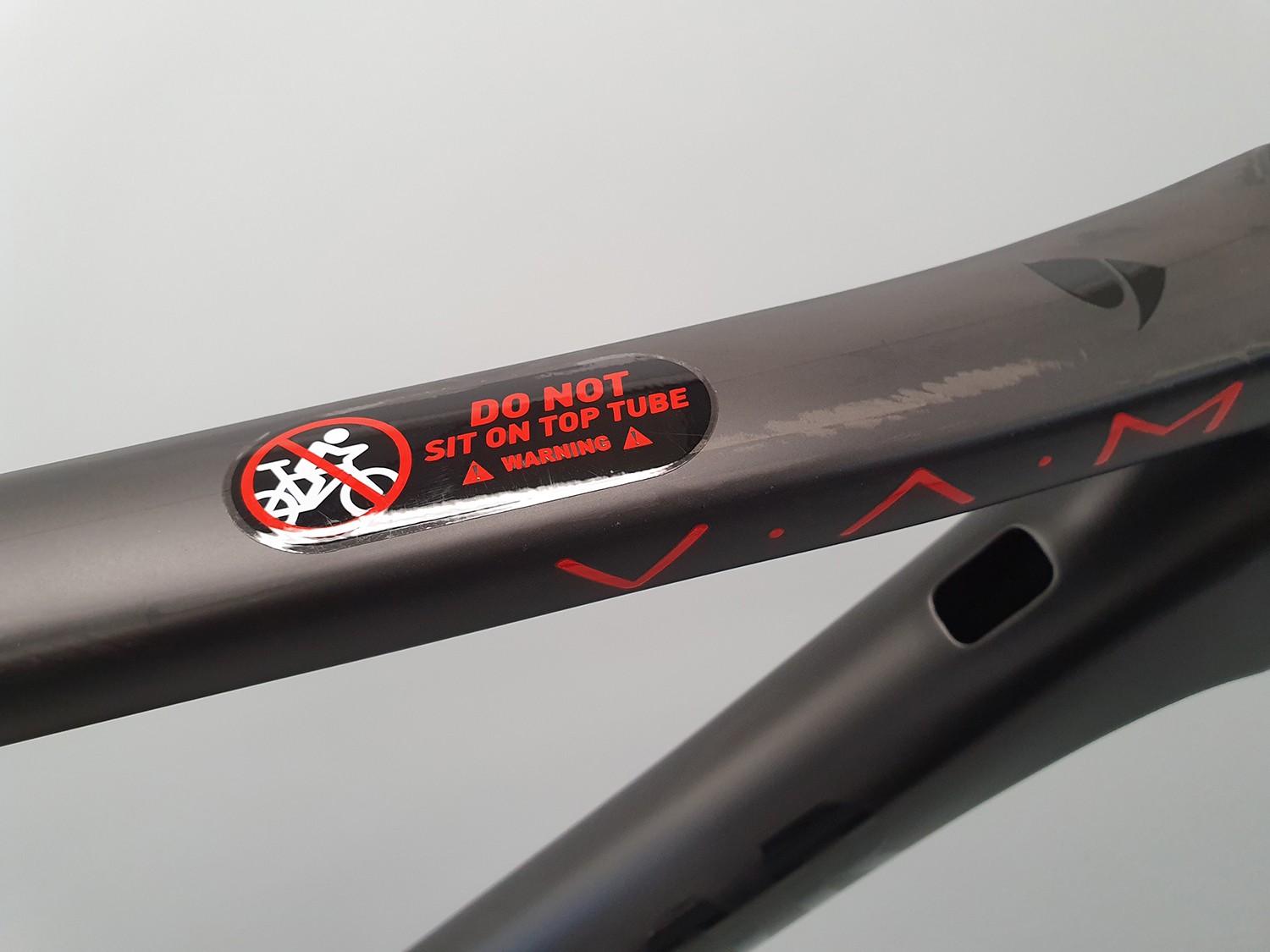
We believe the O2 VAM receives the distinction of being the only production disc road bike to be below the U.C.I. weight limit with a standard build (i.e., no ultralight parts).
From the outside looking in, the O2 VAM looks unassumingly normal for how unconventional it truly is. An initial noticeable difference between the O2 VAM and other ultralights is the sticker “Don’t Sit on the Top Tube.”
Adding the sticker is a tongue-in-cheek nod to the uncommon happening of WorldTour riders crashing due to a cracked top tube after sitting on it. If a top tube cracks in the day-to-day usage, it’s likely due to clamping, the bars spinning around in a crash, or careless handling involving cars, planes or other stationary objects.
What we’re really trying to highlight is loads not related to riding don’t have any place on the top tube of an ultralight race bike. This includes repair stand clamps, trunk-mounted bike racks, and using the top tube as a chair. To quote Phil Gaimon, “It’s a top tube, not a chair!”
Why is the top tube not “stronger”?
When we consider the loads placed on a frame during normal riding the predominant contribution to stiffness comes from the sides of tubes, with the tops and bottoms mostly contributing to hold the sides together, this is how bicycles are able to be made with large openings in the tubes such as MTB’s with tool hiding holes in the frame, and still be ridable. In addition to not contributing too much to the stiffness of the frame, fibers on the top and bottom of a top tube will increase the bike’s vertical stiffness, making it less comfortable to ride.
Because the O2 VAM is unconventional in its engineering, the weight savings come from removing unnecessary materials. All non-structural fibers, or fibers not directly influencing the ride quality, or ISO testing performed for safety reasons, have been removed.
Weight Loads Explained
As you can see from the diagram above, there are no loads on the middle of the top tube. When a bike is stripped of all fibers not directly contributing to the ability to meet the loads seen during normal riding is where issues with sitting on the bike or putting it in a trunk or bad airplane bag can start to happen.
During a traditional, non-optimized layup, the designer still realizes this but needs to address the realities of mass production manufacturability. The sheets of pre-preg fiber need to be quickly applied to the mandrel used for molding the frame and moved through the production process. One of the major challenges in laying up the fibers comes from areas on the frame that have very precise placement of the fibers, vs a larger sheet that can just be slapped on quickly. Take for instance the case at right, where layup operator has a 10×20 sheet of fiber to wrap over the top tube shape on the mandrel.
The easiest and fastest way to do this is to roughly place the sheet in the middle of the frame, and wrap it around the top or bottom of the shape. If the sheet is a little off one way or the other it doesn’t really matter a whole lot as there is plenty of overwrap, and you’ll get enough strength to make sure the bike is safe.
During a traditional, non-optimized layup, the designer still realizes this but needs to address the realities of mass production manufacturability. The sheets of pre-preg fiber need to be quickly applied to the mandrel used for molding the frame and moved through the production process. One of the major challenges in laying up the fibers comes from areas on the frame that have very precise placement of the fibers, vs a larger sheet that can just be slapped on quickly. Take for instance the case at right, where layup operator has a 10×20 sheet of fiber to wrap over the top tube shape on the mandrel.
This approach is effective, and safe, and you will get your desired stiffness, but there is significant extra material that isn’t contributing to the ride experience, which is extra weight. When an optimized layup is used, things like ply overlaps become crucial areas to build up stiffness and minimize weight.
In the example here, you can see that the overlapping areas of the plies have been moved to the sides of the frame, where they have the most impact on stiffness. Further small plies will be added to the sides of the frame only, again, giving the most impact to the riding experience at the minimum possible weight. Again, the primary challenge with these plys are not the ‘engineering excellence’ of putting them in the right place, but its more a function of highly trained staff that are dedicated to the brand and model in question, and are well versed and familiar with the placement of these multitude of small tricky plies of carbon fiber that really make the difference.
When approaching a frame like the VAM, every ply of carbon is evaluated for orientation, drop location, resin type and content, and overlaps. We manufacture this frame in our exclusive factory, with Factor employees laying every ply down. This combination of rigorousness, skill, attention to detail, and expert level layup operators has not been available outside of bespoke and extremely low volume manufacturing before. By applying the principals of manufacturing excellence with attention to detail and know how, we’ve re-established what a light weight frame means.
© 2025 Factor Bikes. All rights reserved / Privacy Policy |Terms