Tech Talk: Internal Cabling Conundrum
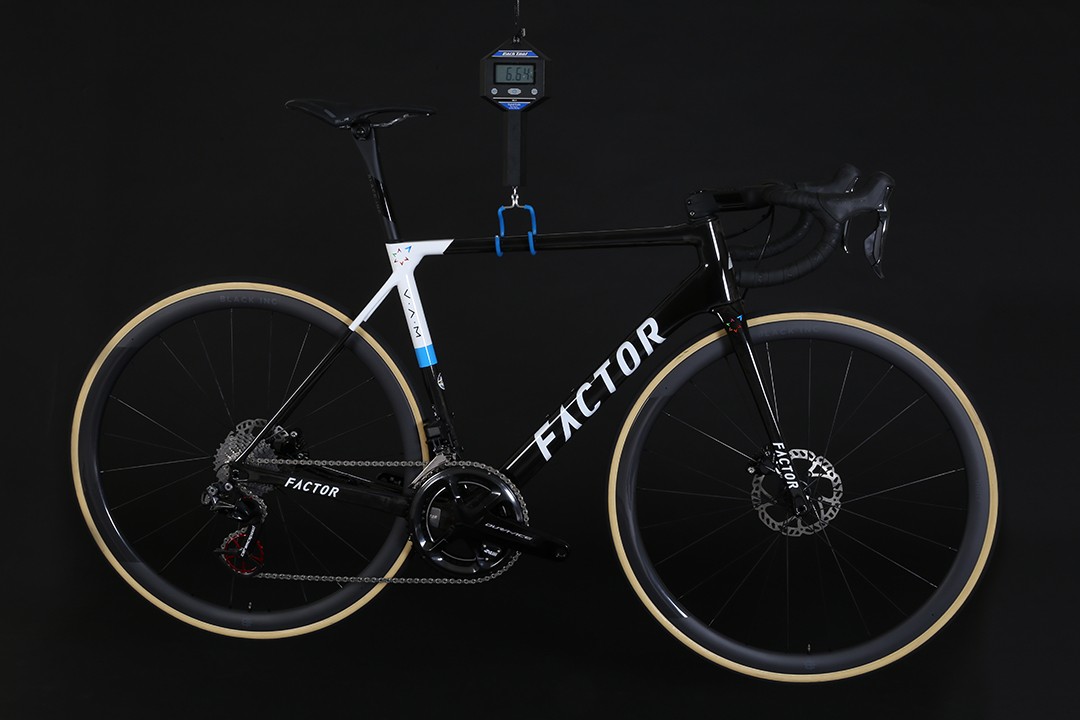
Factor’s Engineering Director, Graham Shrive, explores the ‘ins and outs’ of cable routing when developing a lightweight road frame
Some of our customers have asked why their O2 or O2 VAM has cables showing outside of the frame. To answer this, it is best to explain the product development process and associated challenges around completely hidden cables.
As frame manufacturers, internal cable routing presents one of the biggest challenges when laying out a frame. The advent of disc brakes has given us a great opportunity to start moving towards fully internal cabling. However, there are still a variety of challenges surrounding the complete, shifter to brake, internal routing that becomes paramount when creating a sub 700g frame such as the O2 VAM.
Mechanical Shifting
From the start of the development process of the VAM, we explored whether to include support for mechanical shifting in the frame, with many claiming that it was time to leave it behind. However, when the discussion turned to weight it was quickly noted that the overall Dura-Ace mechanical shifting group is still slightly lighter than the Di2 equivalent. A very relevant discussion point on a bike squarely aimed at our weight-conscious riders.
Once the decision to continue to support mechanical shifting was made, we set about determining the route those cables would need to make to give the rider the best possible shifting performance. Shimano very clearly states that shift housing bends must be executed on radius’ greater than 30mm, at a bare minimum. The challenge with this is that when coupled with the extension of housing into the frame, common in internally routed mechanical systems, the combined effect of friction due to the length of the housing. A tighter radius bend to keep the housing inside of the frame can lead to sluggish shifting under ideal circumstances or worse not shifting at all under non-ideal circumstances. Our solution was to use a replaceable downtube cable stop which allows for bare cables to run fully through the frame from that point, decreasing weight even further, and ensuring crisp shifting and long life.
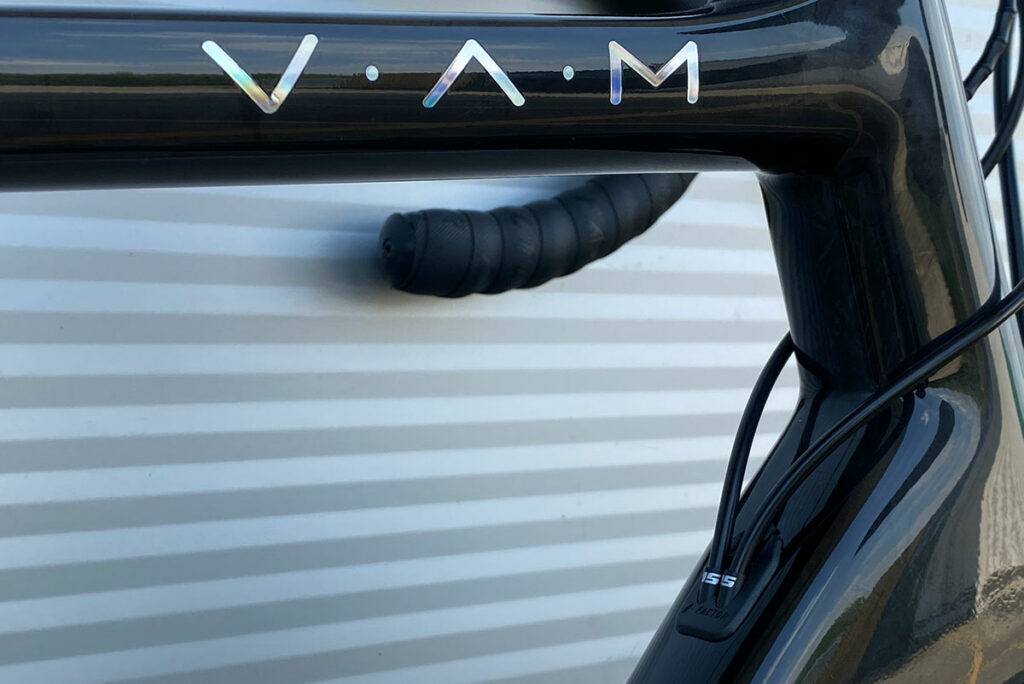
Shimano Di2 & Disc Brakes
When our team evaluated shifting using Di2 and hydraulic hoses, we were extremely conscious of the weight implications when we examined a variety of fully internal routed cabling systems. Typically, these systems rely on oversized upper bearings in the headset and matching oversized split rings. These allow the hoses and wires to enter the frame to the sides, or the front and back of the steerer. This poses a number of challenges, such as the internal routing of the cables through the bar, as well as the fork.
The solutions described above can add as much as 50g to the headset assembly alone. Various hose entry solutions into the front fork leg such as split or pass through preload plugs, contribute to the weight challenges as well. As a system, many current solutions require oversized stems, bars with tremendous grooves in them, multiple hose and wire entry/exits, and the other hardware such as covers and fasteners. All of which contribute to system weight increases of up to 200g.
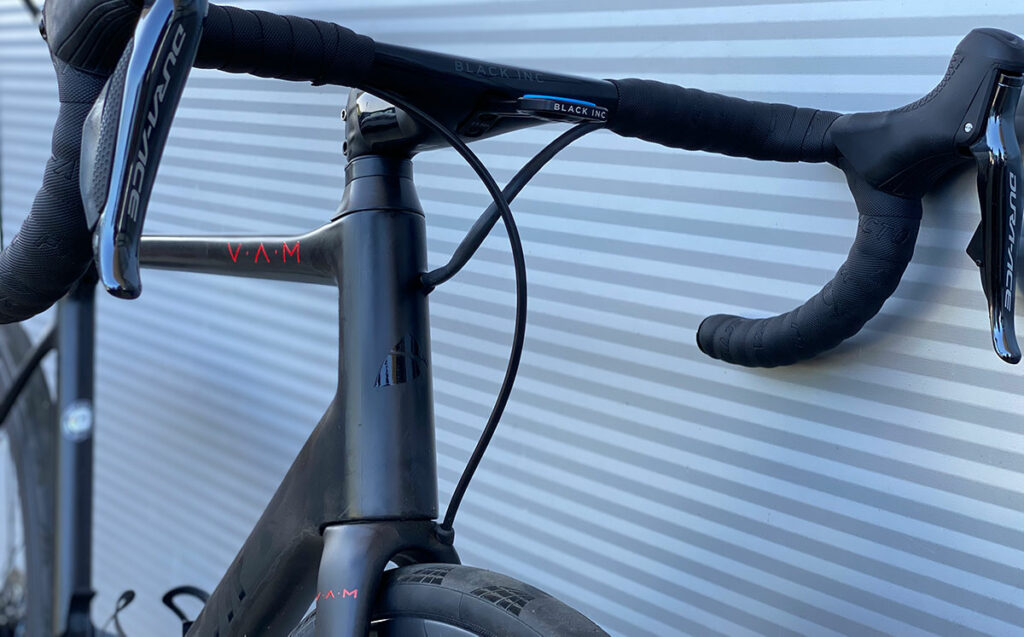
Our ultralight internal routing system fully encloses the cables and Di2 wires from the head tube to the exit at the rear brake, allows for excellent mechanical shift routing and does so at zero added weight.
The Factor O2 and O2 VAM have a shared DNA and are built using the same carbon mould tool. Using ultra-high pressure moulds allow the removal of excessive resin from our base material, making the carbon stronger, lighter and more efficient.
© 2025 Factor Bikes. All rights reserved / Privacy Policy |Terms