Tech Talk: Factor’s Industry Leading Bottom Bracket Solution for the OSTRO VAM
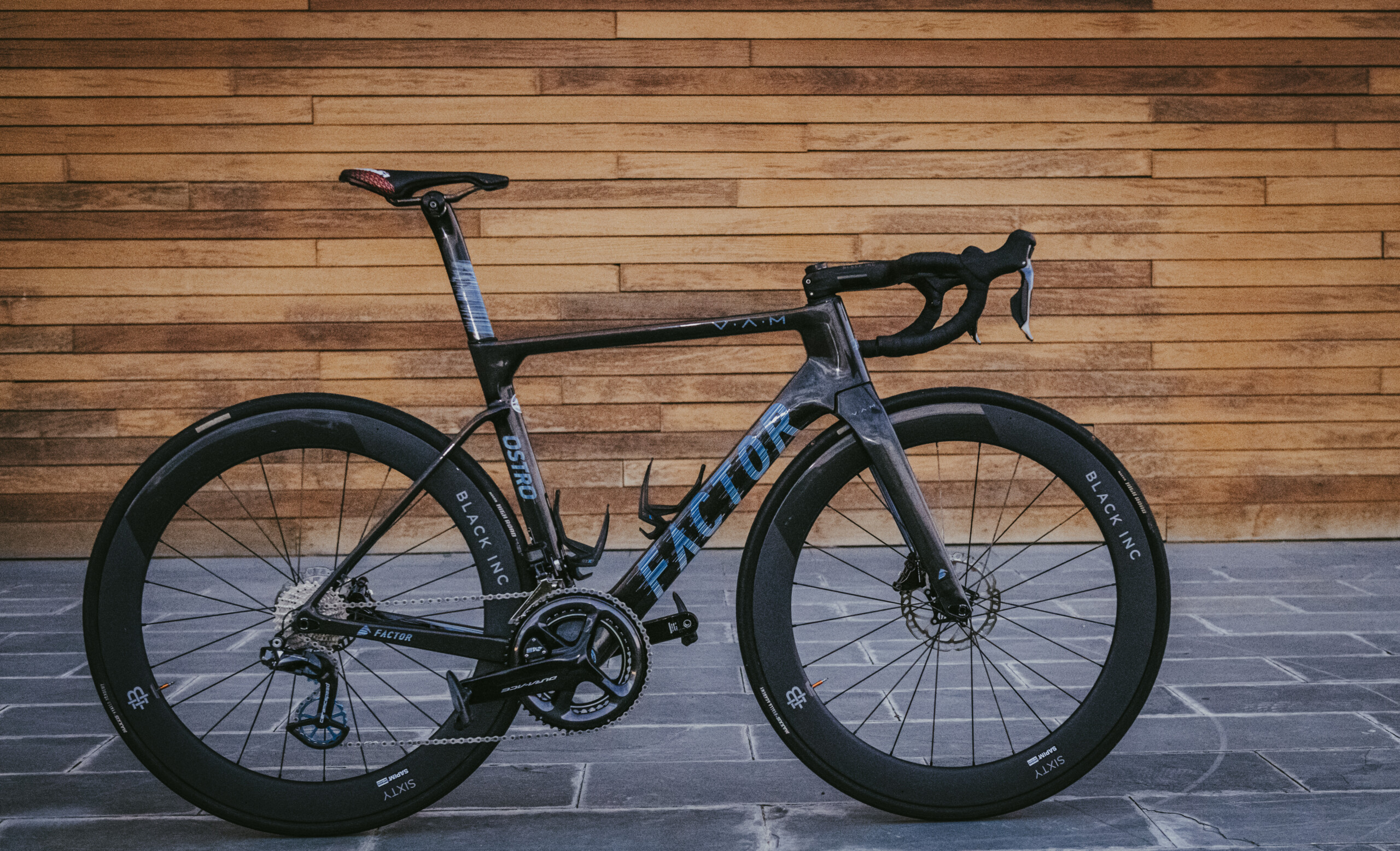
Our Engineering Director, Graham Shrive, discusses the new Bottom Bracket for the Factor OSTRO and explores T47, PF30, BBright, BBcorrect, and now Factor
“New bottom bracket standard” has become something of a dirty phrase in the cycling industry. Over the years, special cranks, rear axles, front derailleur mounts, and even rear wheels have been required to facilitate the various solutions that have been invented by the industry.
When it came to developing a solution for our brand new OSTRO VAM, we listened to current feedback in the market and decided that the best way to serve our riders was to adopt the T47 bottom bracket standard. After years of living with the pros and cons of several of the systems, having ourselves built the first-generation O2 with a PF386 system, we were sure there was a better solution than what the industry was currently providing, so we went looking for it.
Taking a different approach is the ‘Factor way’, and we have proudly developed our own take on the new industry standard T47 bottom bracket. It is based on the existing T47 standard, but adapted to allow for use in asymmetrical frames and is actually co-molded into the frame. Co-molding guarantees that both threaded surfaces will be perfectly in line with one another. The benefit is exceptional bearing life and the lowest possible friction for the crank bearings. We’re also able to save some weight on the frame and maintain current stiffness. To top it off, we have also removed the material between the drive and non-drive side which allows for access to brake hoses and Di2 cables. Mechanics rejoice.
This new industry-leading T47 bottom bracket solution is available on our OSTRO VAM.
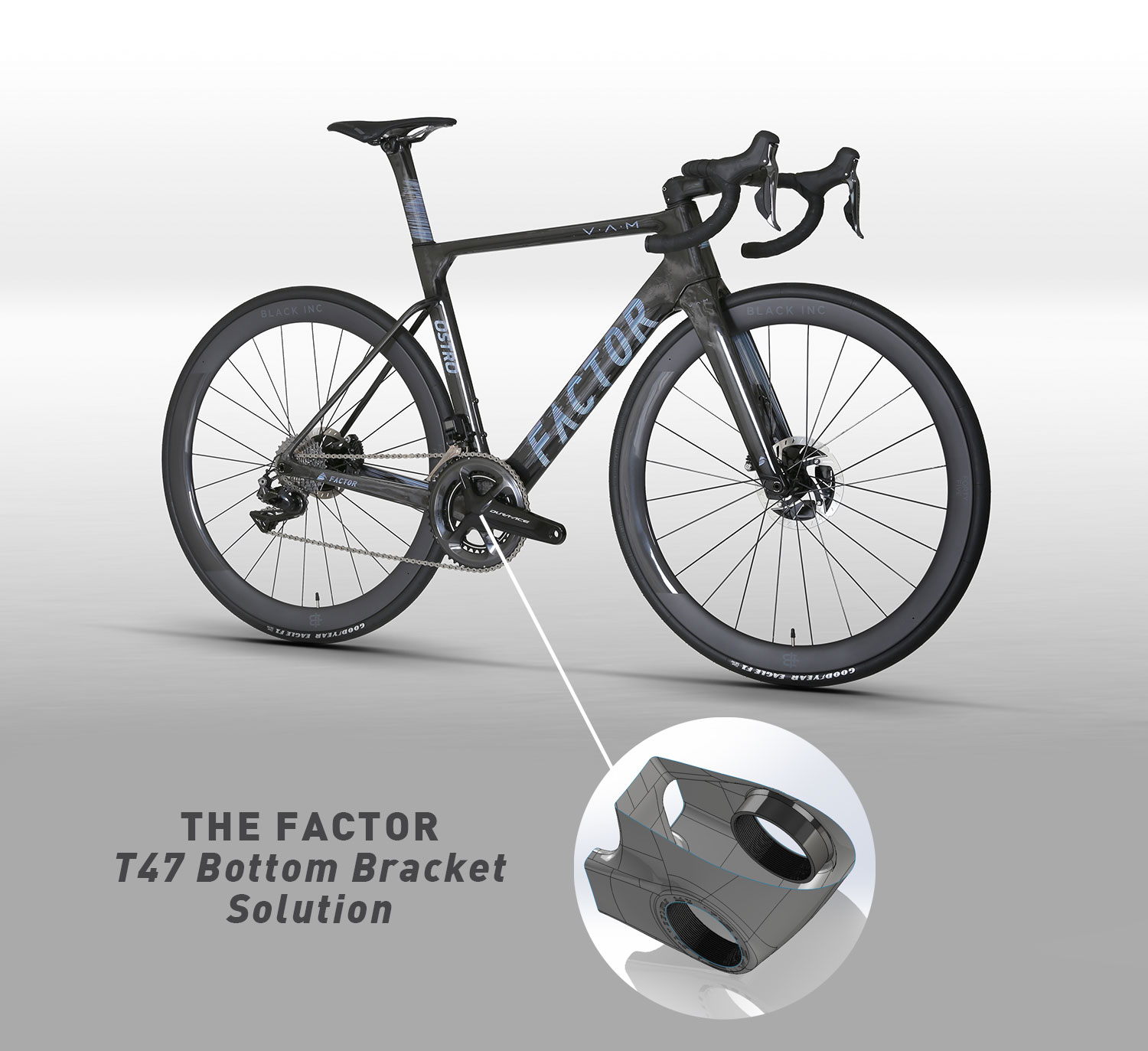
Read on for a deep dive into how we got there:
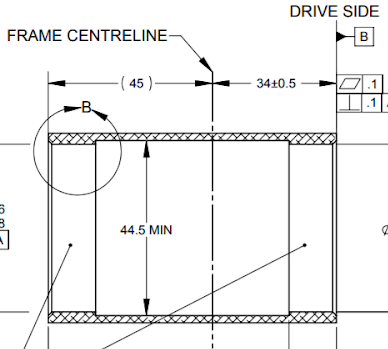
Fig.1 – The BBright standard drawings from BBright.net, as drawn by my former colleague Richard Matthews some 10 years ago. Note the GD&T symbol for the NDS width in parentheses “()” showing that it’s a derived dimension from the total width, which is looking for a tighter tolerance than is typically possible in a production carbon environment
Tolerance Stack
The cumulative effect of the various components in a system’s respective tolerances being combined to be either much larger as a whole, or much smaller, as a whole, than intended. For example, if a frame & BB are on the wider side of their respective tolerances, and a Crank axle on the shorter side, you may get bearing rub.

Fig. 2 – Factor’s ‘BBcorrect’ configuration, found on the ONE, O2-Gen 2, O2 VAM, LS, ViSTA and SLiCK
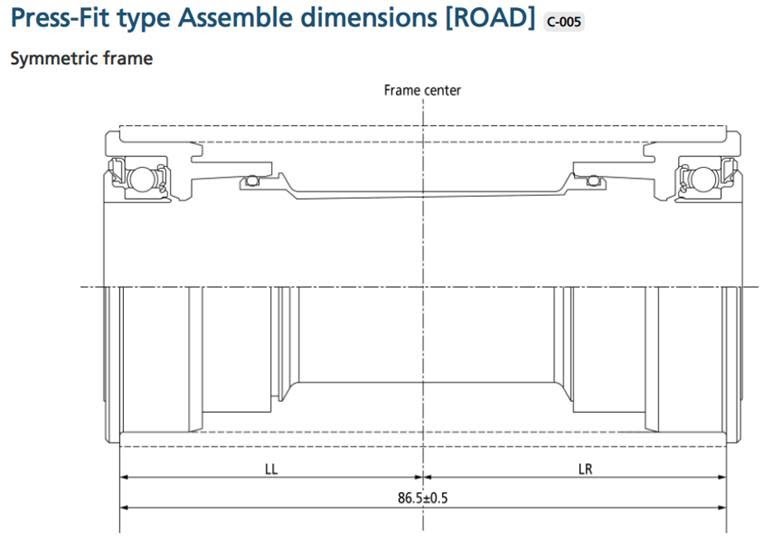
Fig. 3-Shimano Frame design guidance for the BB area
T47 Asymmetrical
The move to T47 was quite straight forward for Factor, given our choices with the ‘BBcorrect’ standard we’ve already started using. By sticking with the 34mm centre to face dimension on the drive side, we’re able to simply use the standard T47-BB30 adapter (T47e). On the non-drive side, we had to do extra homework with our partners at CeramicSpeed, and fortunately, the industry has moved to adopt a universal standard called T47 asymmetrical, which effectively uses the T47i standard. These cups should be readily available from a variety of manufacturers and will fit all makes and models of BBs, such as Campagnolo Ultra-Torque, SRAM’s Dub system, Shimano 24mm, and native 30mm cranks.
By working with T47 asymmetrical, we also have the benefit that our current frames match the width of the practical maximum for current road cranks, which is also what the T47 asymmetrical standard is set at. By objectively evaluating the needs of the rider and balancing these with the practical constraints on BB width imposed by the various crank standards, we were able to adapt to the current shift to T47 frames with our current ‘BBcorrect’ configuration and offer both T47A and PF4630 frames from the same mold. As seen by our WorldTour team, Israel Start-Up Nation who used press fit versions of our new OSTRO VAM at the Tour de France.
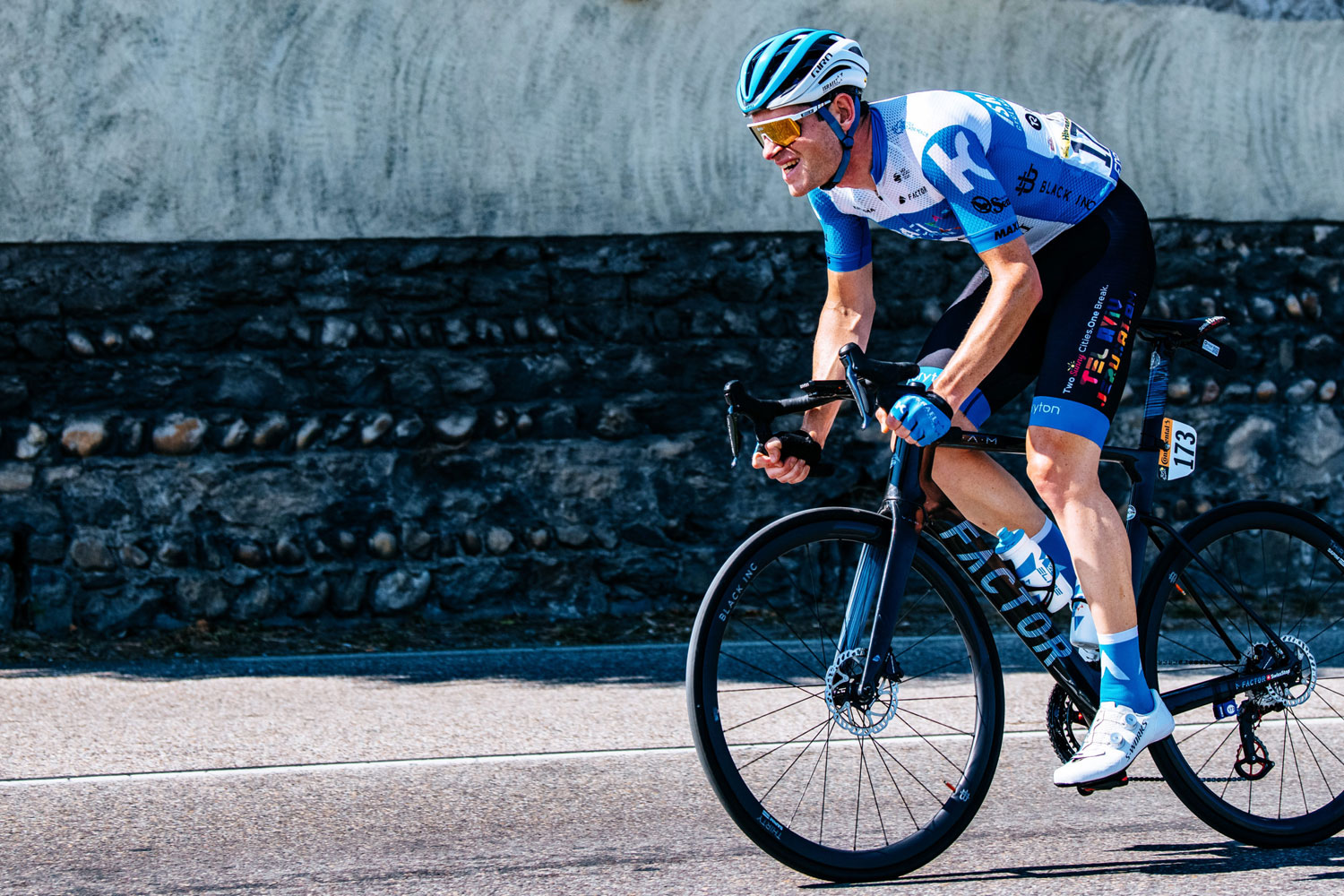
The Factor Difference
When you choose Factor, you know that you are choosing a brand that takes a different approach. This of course applies to our approach with the T47 BB standard. Most manufacturers using T47 are adopting a typical overlapping bonded bottom bracket using a flat interface with the frame and then bonding the cups together in the middle of the section. When used most effectively, this design relies on a positive interface between the frame itself and the bb shell. Typically, this is composed of some type of non-structural material built up on the inside surface of the frame, which is partially machined away and then also bonded to the overlapped sleeves. This approach adds significant amounts of non-structural material in the overlapping cups, as well as the built up area of the frame, which of course is extra weight.
In addition, when we examined this typical way of constructing a T47 BB interface, one of the primary impediments was the actual width of the frame flange interfaces, which added as much as 3mm of unneeded aluminium to each side of the frame, reducing the amount of real estate available to us to improve frame stiffness. Also, the large concentration of stress at the face transition of the flanged surface and the frame can lead to significant concentrations of peel stress. When this surface is finished or painted, this stress can manifest itself in paint cracks or outright debonding of the BB sleeve.
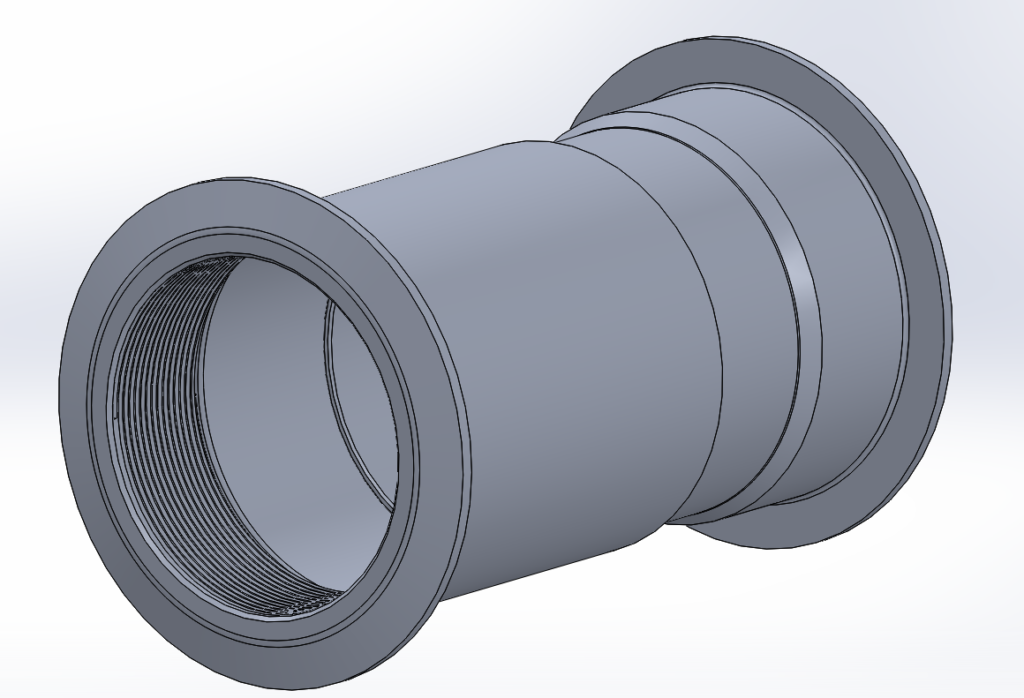
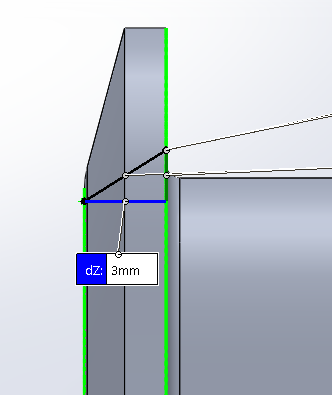
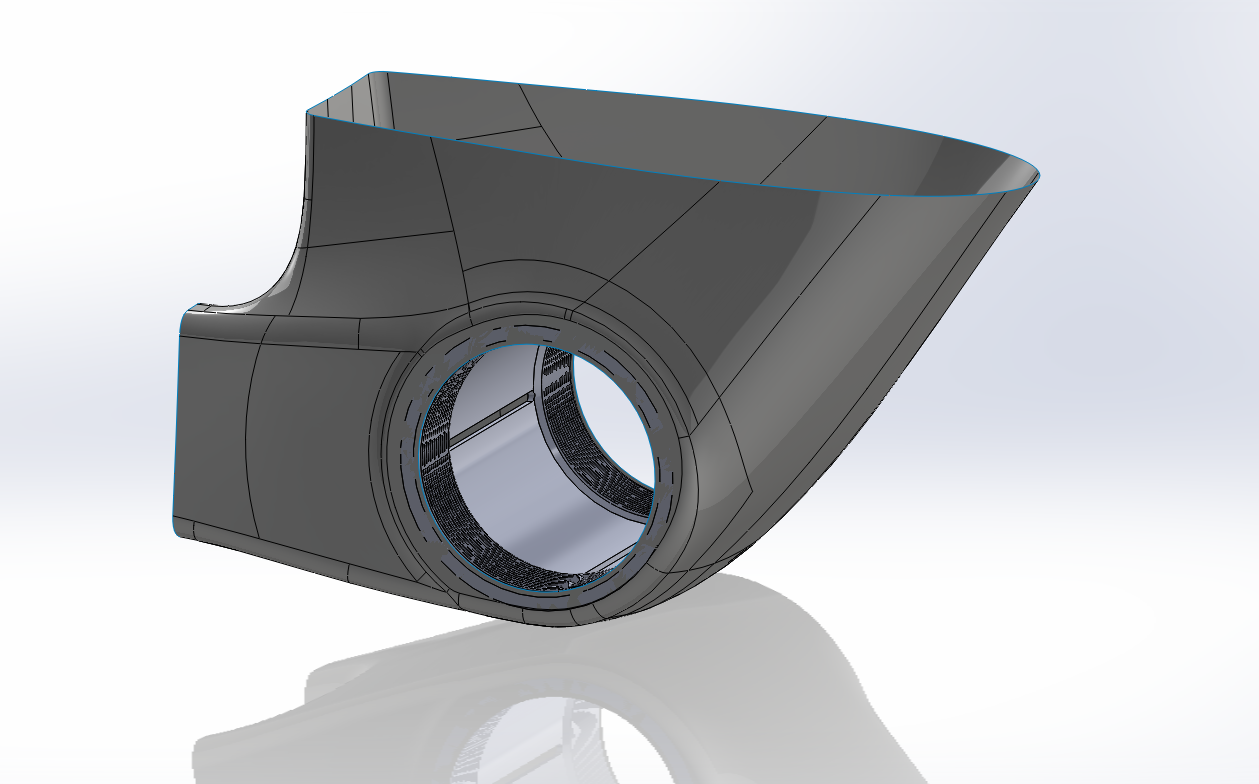
Fig. 7 – Co-molded BB Sleeve pre-machining
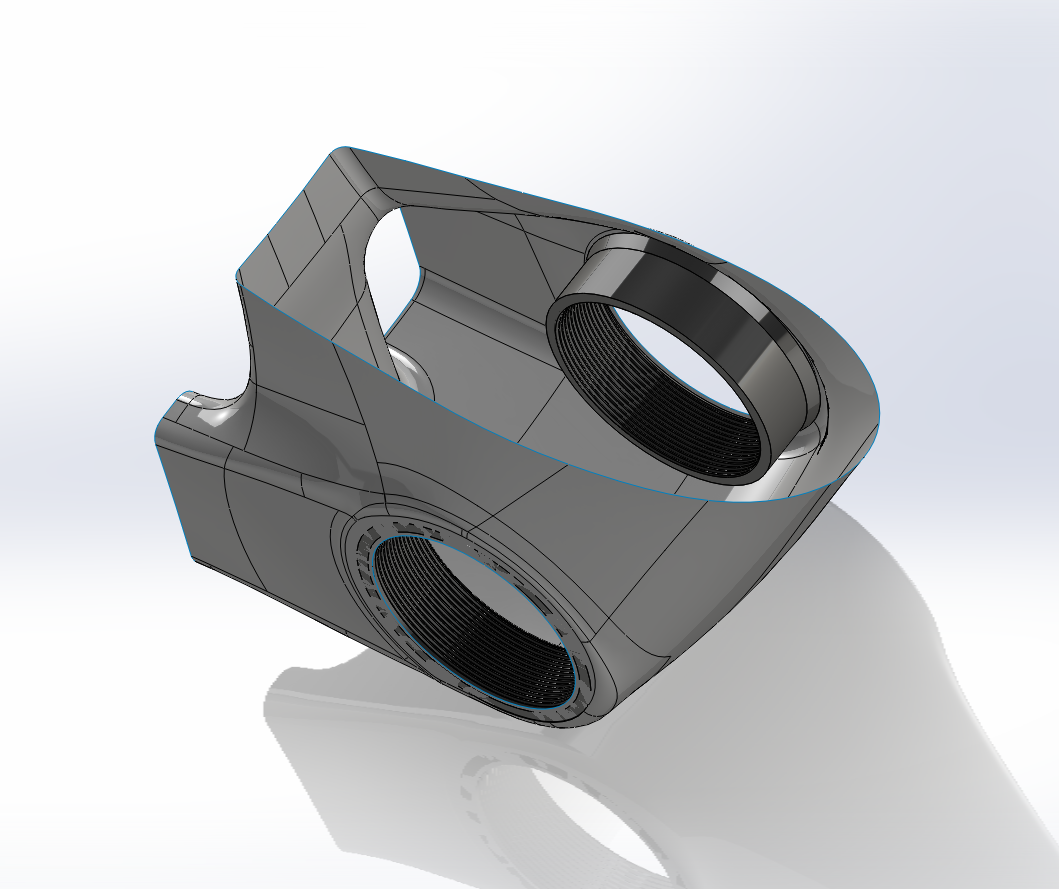
Fig. 8 – Finished T47 BB interface
© 2025 Factor Bikes. All rights reserved / Privacy Policy |Terms